PiMC (Powder in-Mould Coating) are products that have been specially developed for the surface coating and finishing of SMC/BMC components. Our powder coatings on the basis of unsaturated polyester resins are filled with glass beads in order to enable high-resistance surfaces.
The material in powder form is first applied in layers to the hot tool surface. This takes place electrostatically either manually or automated at a thickness of 150 to 250 microns. The SMC/BMC substrate can subsequently be inserted directly into the tool after which the pressing procedure can start immediately. Because both the PiMC products and the SMC/BMC materials consist of unsaturated polyester resins, both components have an identical cross-linking reaction during the moulding process. This creates an inseparable, chemical bond between the surface and carrier substrate during the curing phase. Additionally, the PiMC coating simultaneously hides all SMC/BMC-typical surface errors such as fibre textures or porosities. At the end of the pressing process, the finished component can be removed from the mould analogue to the typical SMC/BMC processing technology.
The big advantage for customers is that additional, complicated process steps, such as the application of primers, fillers or paint, are unnecessary, because a homogeneous, highly resistant surfaces is already formed during the PiMC process. PiMCs can, of course, be displayed in a very wide, customer-specific colour spectrum.
With our basic formulations, you provide the coated SMC/BMC component a scratch and abrasion-resistant surface, which is also resilient to chemicals, UV light and weathering.
For special applications, our PiMC products are also available with special properties for vibrant, high gloss optics, to create a luxurious granite or metallic effect. Grades with graffiti-resistant surfaces, approval for contact with food as well as with anti-microbacterial properties are also available.
Special environmentally friendly, halogen- and phosphorous-free, self-extinguishing versions fulfil the testing requirements according to the highest (fire protection) hazard class (HL 3) of EN 45545.
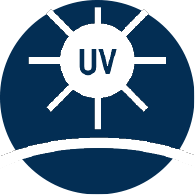
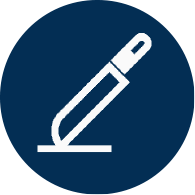
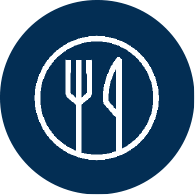
Applications
The PiMC process is extremely efficient and economical, because it enables you to produce SMC/BMC components with outstanding, functionalised surfaces with little technical effort. For many years, our products have been demonstrating their excellent performance. This includes a wide range of applications such as the manufacture of chemically and mechanically highly stressed kitchen sinks, scratch-resistant, graffiti-resistant and flame-resistant seats in public transport vehicles and stadiums with weatherproof properties, also for electrical cabinets in outdoor areas.
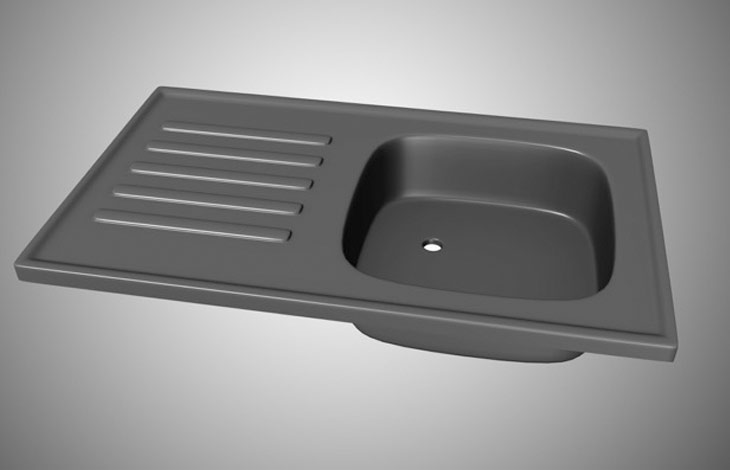
Kitchen sinks
with individual design options
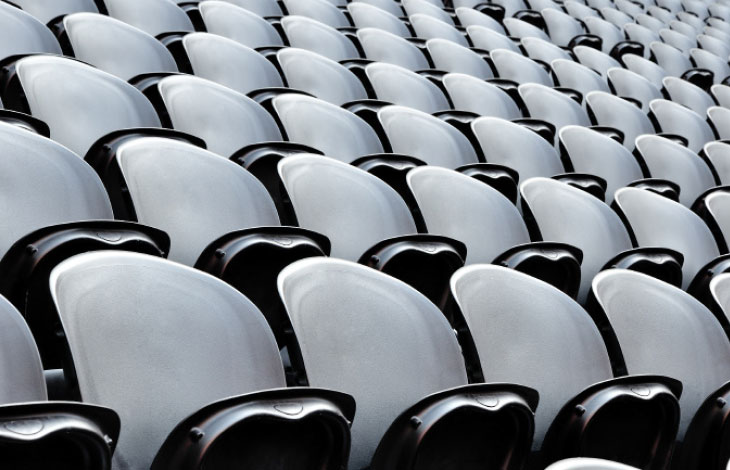
Stadium seats
with weather-resistant properties